Wholesale Dealers of Custom Precision Milling Parts - Surface coating – Neuland Metals
Wholesale Dealers of Custom Precision Milling Parts - Surface coating – Neuland Metals Detail:
Surface coating
The surface coating process includes painting, powder coating, Electro-painting, Anodizing, zinc plating, hot galvanizing, electroless nickel plating and so on according to customer requirements. The function for the surface treatment is to prevent rust and corrosion in certain environment.
The surface coating process includes powder coating, Electro-plating, Anodizing, hot galvanizing, electro nickel plating, painting, and so on according to customer requirements. The function for the surface treatment is in an effort to prevent corrosion or simply improve appearance. In addition, some of these treatments also provide enhanced mechanical or electrical properties that contribute to the overall functionality of the component.
Powder coating or spraying – With this type of treatment, the metal parts need to be preheated to a required temperature and then to dip the part into fluidized bed or to spray the powder on the part. With post curing, it depends on the specific property of the powder.
The powder used normally are resin epoxy material or Rilsan.
Electroplating – This process forms a thin metallic coating on the substrate. The electroplating process passes a positively-charged electrical current through a solution containing dissolved metal ions and a negatively charged electrical current through the metallic part to be plated. Common metals utilized for electroplating are cadmium, chromium, copper, gold, nickel, silver, tin, and zinc. Almost any base metal that conducts electricity can be electroplated to enhance its performance.
Chemical Treatment – This method involves processes that create thin films of sulfide and oxide by means of a chemical reaction. Typical uses are for metal coloring, corrosion protection, and priming of surfaces to be painted. Black oxide is a very common surface treatment for steel parts and “passivation” is used to remove free iron from the surface of stainless steel parts.
Anodic Oxidation – This type of surface treatment is typically used for light metals, such as aluminum and titanium. These oxide films are formed by electrolysis, and since they are porous, dyeing and coloring agents are frequently specified for an improved aesthetic appearance. Anodization is a very common surface treatment that prevents corrosion on aluminum parts. If wear resistance is also desirable, engineers can specify a version of this method that forms a relatively thick, extremely hard, ceramic coating on the surface of the part.
Hot Dipping – This process requires the part to be dipped into dissolved tin, lead, zinc, aluminum, or solder to form a surface metallic film. Hot-dip galvanizing is the process of dipping steel into a vessel containing molten zinc. Used for corrosion resistance in extreme environments, guard rails on roads are commonly processed with this surface treatment.
Painting – Surface treatment painting is commonly specified by engineers to enhance a part’s appearance and corrosion resistance. Spray painting, electrostatic painting, dipping, brushing, and powder coat painting methods are some of the most common techniques used to apply the paint to the surface of the component. There are many types of paint formulations to protect metal parts in a wide range of physical environments. The automotive industry has automated the process of painting cars and trucks, utilizing thousands of robot arms and producing extremely consistent results.
Product detail pictures:




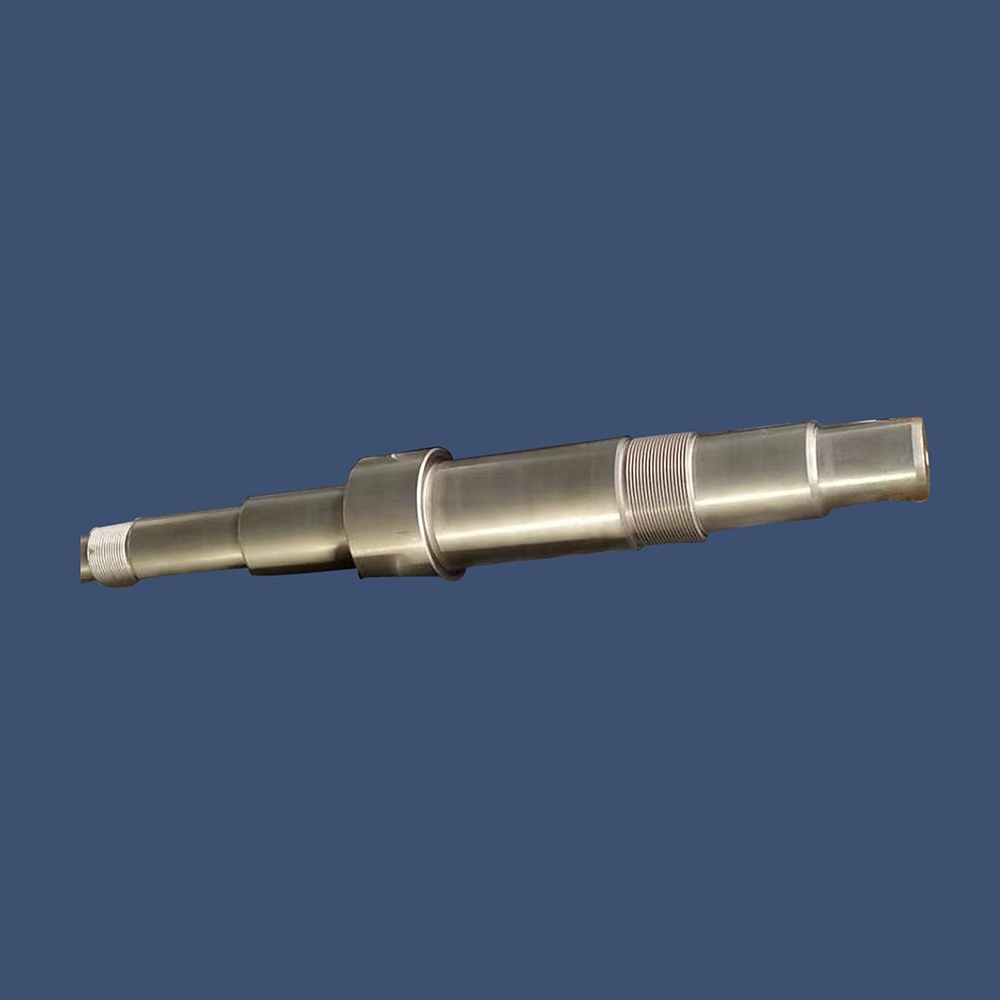



Related Product Guide:
We normally think and practice corresponding towards the change of circumstance, and grow up. We aim at the achievement of a richer mind and body plus the living for Wholesale Dealers of Custom Precision Milling Parts - Surface coating – Neuland Metals , The product will supply to all over the world, such as: Hanover, kazan, Washington, We have 48 provincial agencies in the country. We also have stable cooperation with several international trading companies. They place order with us and export products to other countries. We expect to cooperate with you to develop a larger market.

Sales manager is very enthusiastic and professional, gave us a great concessions and product quality is very good,thank you very much!
